Confluence
Washington, D. C.
Taylor Caldwell
Construction, BAE/MAE
Adviser: Ray Sowers

Building Statistics:
General Building Data
Building Name |
Location |
Occupancy Type |
Size |
Stories |
Dates of Construction |
Building Cost |
Project Delivery Method |
Confluence (fictitious)
Buzzard Point, Washington, D.C.
Renovated Mixed-Use Community
Residential & Retail
729,294 SF
Parking - 186,284 SF
Retail - 71,783 SF
Residential Amenity - 25,979 SF
Residential Units - 445,248 SF
9 Total Levels
8 Stories Above Grade
2 Stories Underground Parking
July 2018 - December 2020
$112.75 M
Negotiated Design-Bid-Build
Meet Confluence's Team
Architecture
Confluence is a renovation project. The building was originally built in 1971, and its previous use was the United States Coast Guard Headquarters. It is currently designed to be a luxury apartment building in the Buzzard Point area of Washington, D. C. The ground level is shared between five restaurant spaces as well as residential amenity space and lobby entrances to the upper story residential units. Continuing up the building, the Third Level will have residential amenity space and units, and the fourth through the eighth level will have units. The Penthouse Level will consist of residential units, amenity space, and a rooftop pool, seen in Figure 1. There are 480 residential units in total. In addition, there are two existing below-grade parking levels. The design, orientation, and massing of Confluence are based on the adaptive reuse of the existing building, which requires carving out four residential courtyards starting with Third Level to maximize articulation and views for residents and visitors.

Figure 1*: Rooftop Pool
Applicable Codes
DCMR Title 11 – Zoning Regulations 2016 (ZR16); Title 12 DCMR, DC Construction Codes Supplement (2013); 2013 District of Columbia Building, Property Maintenance, Green Construction, Energy Conservation, Fire, Mechanical, & Plumbing Codes; 2011 National Electric Code
CG-5 (Capitol Gateway)
National Codes:
Zoning:
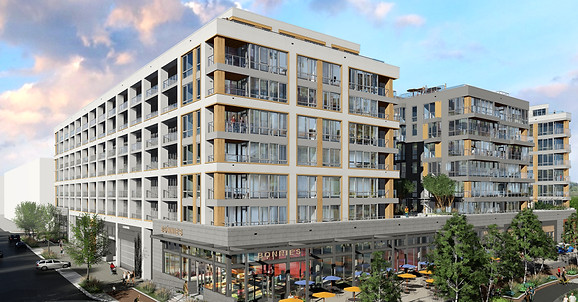
Figure 2*: South Elevation
Building Enclosure
Confluence will incorporate high quality materials and a color palette that marks the property as a destination in its growing Buzzard Point neighborhood. It includes retail entrances located all around the property and two residential lobbies connected with indoor residential amenities that divide the plan into north and south retail areas. A rendering of the south retail can be viewed in Figure 2.
The building façade consists of many different types of materials. The ground level, which the majority will be restaurant storefronts, consists of a cast-in-place concrete curb with low-emissivity-coated, insulated glass unit storefronts. The IGU, low-E-coated will also be the residential window walls. The residential terrace dividers will use monolithic, acid etched, fully tempered glazing. The remainder of the building will be encased with either metal composite material wall panels (MCM), aluminum-faced composite wall panels (ACM), or high-density fiber cement panels. A typical Fiber Cement wall panel detail can be viewed in Figure 3.
Building Façade

Figure 3*: Wall Detail


Architecture
Confluence is a renovation project. The building was originally built in 1971, and its previous use was the United States Coast Guard Headquarters. It is currently designed to be a luxury apartment building in the Buzzard Point area of Washington, D. C. The ground level is shared between five restaurant spaces as well as residential amenity space and lobby entrances to the upper story residential units. Continuing up the building, the Third Level will have residential amenity space and units, and the fourth through the eighth level will have units. The Penthouse Level will consist of residential units, amenity space, and a rooftop pool, seen in Figure 1. There are 480 residential units in total. In addition, there are two existing below-grade parking levels. The design, orientation, and massing of Confluence are based on the adaptive reuse of the existing building, which requires carving out four residential courtyards starting with Third Level to maximize articulation and views for residents and visitors.

Figure 1*: Rooftop Pool
Applicable Codes
DCMR Title 11 – Zoning Regulations 2016 (ZR16); Title 12 DCMR, DC Construction Codes Supplement (2013); 2013 District of Columbia Building, Property Maintenance, Green Construction, Energy Conservation, Fire, Mechanical, & Plumbing Codes; 2011 National Electric Code
CG-5 (Capitol Gateway)
National Codes:
Zoning:
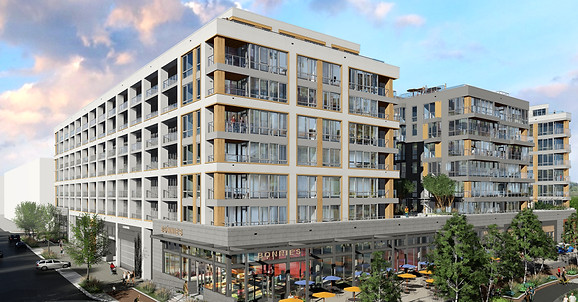
Figure 2*: South Elevation
Building Enclosure
Confluence will incorporate high quality materials and a color palette that marks the property as a destination in its growing Buzzard Point neighborhood. It includes retail entrances located all around the property and two residential lobbies connected with indoor residential amenities that divide the plan into north and south retail areas. A rendering of the south retail can be viewed in Figure 2.
The building façade consists of many different types of materials. The ground level, which the majority will be restaurant storefronts, consists of a cast-in-place concrete curb with low-emissivity-coated, insulated glass unit storefronts. The IGU, low-E-coated will also be the residential window walls. The residential terrace dividers will use monolithic, acid etched, fully tempered glazing. The remainder of the building will be encased with either metal composite material wall panels (MCM), aluminum-faced composite wall panels (ACM), or high-density fiber cement panels. A typical Fiber Cement wall panel detail can be viewed in Figure 3.
Building Façade

Figure 3*: Wall Detail

Figure 4*: Green Roof Detail
The main roof will consist of a green roof to comply with the zoning regulations. The green roof assembly, seen in Figure 4, will consist of 6” of EcoCline Green Roof, a filter fabric, 2” of mineral wool board insulation, and 4” of XPS insulation on top of a protection sheet and hot fluid-applied waterproofing on the structural deck. For general roof spaces like the terraces, the assembly will consist of stone ballast, filter fabric, XPS insulation, a TPO protection board, and hot fluid-applied waterproofing on the structural deck/substrate. The remaining canopy locations will use polyvinyl-chloride (PVC) roof membrane. A view of the overall roof can be seen in Figure 5.
Roofing
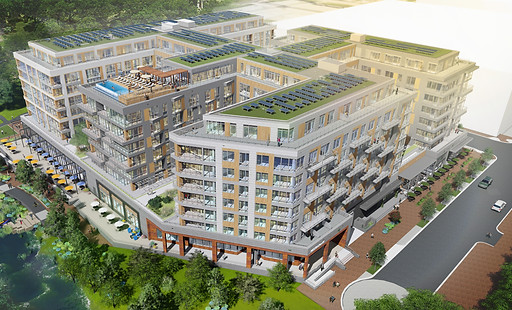
Figure 5*: Solar Roof
Sustainability
Designed to recycle and reuse efficiently, Confluence targets LEED Gold certification. The community will be constructed to include a solar-paneled roof, a plumbing system with 20 percent water usage reduction, water-saving toilets, energy efficient lighting fixtures, and EnergyStar appliances. Confluence also promotes sustainable transportation given its walking distance to nearby businesses and attractions, electric charging stations, and bike storage facilities. Figure 6 shows how the solar panels will be incorporated into the green roof.

Figure 6*: Solar Roof Panels
*Note: All figures/images are courtesy of Antunovich Associates and their Drawings Sets
Construction
Demolition
Demolition was a huge aspect for Confluence to begin. The original structure had eight full above-ground stories of concrete slabs. An aspect to Confluence’s design is four courtyards cut into the building, elevated to the Third Floor. This started by removing areas of the existing slab starting with the Third Level and continuing above through the existing roof level. In addition, the majority of the Second Level was removed to achieve double-height ceilings for the Ground Level as requested by the restaurant retailers. In addition, the existing roof (the current Penthouse Level floor) was removed due to structural concerns.
MEP System
Considering that Confluence is located right along the river, the electrical equipment was required to be elevated above the 500-year flood plan. To accomplish this, a concrete pad was elevated five feet off the Ground Floor level to house the generators. For the main electrical room, it was engineered to leave a section of the Second Level without being demoed to hold to this room.
Lighting / Electrical
Electrical
Confluence’s electrical service will originate from PEPCO-maintained on-site transformer vaults located near the east properly line. The electrical services that have been approved by PEPCO are as follows:
-
(2) Commercial house service 4,000 AMP, 460 Volt, 3-phase services
-
(1) Commercial house service 3,000 AMP, 460 Volt, 3-phase service
-
(2) Residential service 2,000 AMP, 460 Volt, 3-phase services
-
(1) Residential service 1,600 APM, 460 Volt, 3-phase service
To step down the 460V residential service to the code-required 208V for residential dwelling units, three large dry-type transformers (two 1,500 kVA, one 1,000 kVA) will be provided in the main electrical room.
In addition to the main electrical room on the Second Level, there are two electrical rooms per residential floor.
Lighting
The lighting for Confluence’s amenity areas has been inspired by Scandinavian influence. The lighting plays with the scale and color, and it becomes the focal points within these spaces. For example, the lighting fixtures in the fitness center are suspended and hung at varying angles to maintain a fresh and clean aesthetic with an energetic twist.
For the unit doors in the corridors, there is an indirect light cove at each door drop to enhance the rhythm of the corridors, making the doors the focal points. For all unit lighting, LED fixtures will be used to reduce the energy usage and help to achieve the project LEED Gold goal.
Mechanical
For the mechanical systems, Confluence will house multiple different types. For the residential junior and studio units, the HVAC systems will consist of ceiling mounted, ducted, VRF fan coil units connected to ceiling mounted branch selector boxes located in the corridors. These will then be connected to condensing units located in mechanical rooms throughout the building. For the remainder of residential unit types and amenity spaces, three DOAS units housed on the Penthouse level will provide air quality. Each residential unit will have individual, wall-mounted programmable thermostats.
Retail spaces will have the availability to connect VRF fan coils units to the condensing units provided in mechanical spaces in the loading areas, if they choose, however, their mechanical systems are still being discussed as it is outside of the General Contractor’s scope of work.
Below grade parking as well as the Ground Level will be mechanically ventilated using exhaust fans that are connected to carbon monoxide controls. These fans are ducted out through the Northwest courtyard.
Structural
Existing Structure
Tie - Downs
The existing Confluence structure consisted of two below-grade concrete levels and eight above-grade concrete levels. The structure was supported on a (30) inch thick mat foundation.
To prevent uplift of the building against the water pressure of a potential flood, (223) micropile tie-downs were installed in the mat foundation at the second level of underground parking. These were added in the footprint of the courtyards removed at levels above.
Cast - in - Place Concrete
Even though the existing structure was concrete, the concrete scope covered multiple aspects for Confluence since the changing of building function affected the structural loads. As explained in the Demolition section, the Third Floor courtyard slabs were removed. These areas were re-poured with a ten-inch thick slab with (5.5)-inch thick drop panels at each column location. Each column supporting the courtyards was removed and re-poured in a larger size. To accommodate the removal of the Second Level slab, all columns in these double-height ceiling spaces were strengthened by enlarging the columns on each side with concrete and rebar. The remainder of existing columns on upper level floors were re-used excluding all perimeter columns on the Eighth Level; these were removed and re-poured at the same size with higher concrete strength.
In addition to the tie-downs, a three-inch concrete topping slab was added on top of the mat foundation to also resist against potential uplift forces as well as repair existing slab damage. The existing roof slab (current Penthouse Level floor) was replaced with a (12)-inch thick conventional concrete slab as well as an eight-inch thick topping of normal weight concrete.
One new bay was added at the south side of the building from the Ground Level to the Penthouse Level. This consisted of an eight-inch thick concrete slab supported by concrete beams ranging from (20) to (24) inches. This extended bay was supported by newly poured concrete columns on each level.
Shear Walls
Structural Steel Frame
New shear walls were added from the top of the mat foundation to the underside of the Seventh Floor to resist the lateral forces when demolishing the four courtyards.
The majority of the building is existing concrete, however, a new Penthouse Level needed to be added. For this, structural steel columns and beams were used; these beams varied in depth from (12) to (14) inches. For the new roof level, a (3.25)-inch thick light weight concrete slap was poured on top of a three-inch thick steel deck. Moment frames were added to resist the lateral forces.