Confluence
Washington, D. C.
Taylor Caldwell
Construction, BAE/MAE
Adviser: Ray Sowers
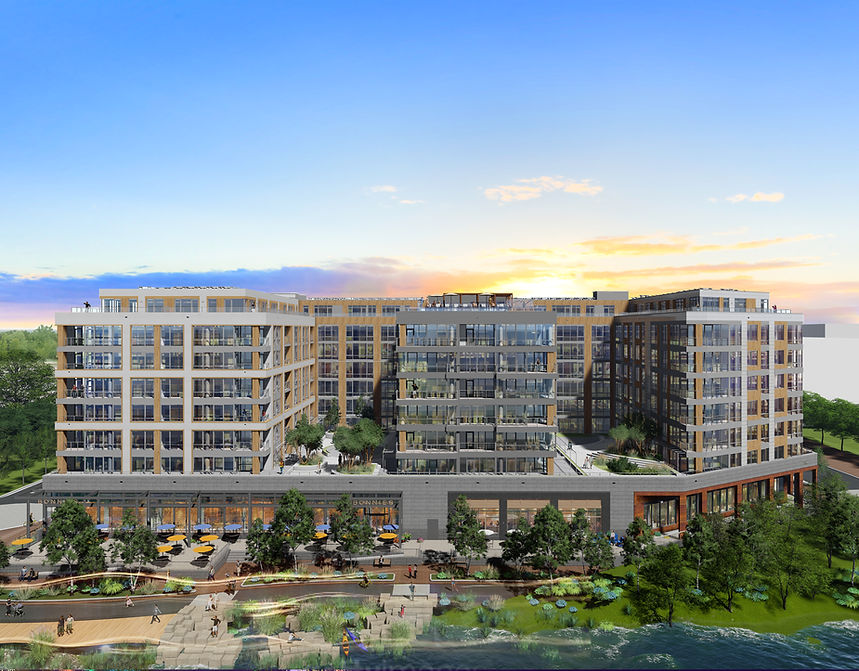
EXECUTIVE SUMMARY
Confluence is a mixed-use renovation project located in Buzzard Point, Washington, D.C. It will feature 480 apartment units, five restaurant spaces, and several amenity spaces. The structure is eight existing concrete floors with two additional levels of underground parking; it will have an additional penthouse steel level once complete. The 729,294 square foot project will take approximately 30 months to complete. The project is being constructed by CBG Building Company with a contract value of $112.75 million. Four separate analyses were conducted on various aspects of Confluence in an attempt to improve the overall cost, schedule, or constructability. The following sections summarize the analyses’ findings presented later in this report.
Analysis 1: New Construction vs. Renovation
Upon investigation, it was noted that there was excessive demolition and structure reinforcing for the current renovation project. Therefore, Confluence was analyzed as a new construction project; this was compared to the current renovation project. A structural breadth was created to assist with developing the new construction aspect by developing two different bay types to represent the spaces of the building. Both a renovation and new construction estimate, including demolition, were created using RS Means data. It was found that the new construction project would cost $2.3 million more than the current renovation, a 2% increase of the total building cost. For the schedule, the new construction would save 41 days for the demolition and structure portion of the project, a 6.5% overall schedule decrease assuming that this work was on the critical path. Because of these factors as well as more freedom for the designers, it was recommended that Confluence be built as new construction rather than renovation.
Analysis 2: Eliminating Discrepancies with Laser Scan
A large issue with renovation projects is discovering issues between the drawings and the existing conditions, as is the case for Confluence. Because of the change orders and schedule reworks, the project was analyzed as if the structure had been laser scanned prior to non-structural construction but after demolition. Laser scanning and modeling quotes were obtained to understand the cost and timeline of adding this procedure to Confluence. Comparing to the change order cost from the discrepancies, laser scanning would save approximately $360,000 for the project. For the schedule, adding laser scanning into the timeline once the structure was gutted would have no significant schedule impacts. This analysis also includes a plumbing breadth. Stemming from another issue was found between the drawings, the current Ground Floor sanitary pipe was conflicting the retailers’ height requirements. An additional outlet was discovered after construction began, so this breadth analyzed rerouting the piping to use the newly discovered outlet. This reroute has a height savings for the retailers, which further indicates that laser scanning would be beneficial for Confluence. Because of the items indicated, laser scanning the existing structure was recommended for Confluence.
Analysis 3: Implementation of SIPS for Residential Units
Upon analysis, it was noted that the schedule for the residential unit construction was somewhat lengthy and random. To potentially improve this, a Short Interval Production Scheduling matrix was. To create the SIPS matrix, sections of the building were designated. It was determined that there would be 35 total sections, seven on each level for Floors 4 through 8. The production of the activities was calculated by using the actual durations and the observed crew sizes. With this, it was determined that each activity would complete each section in two days, and the full SIPS matrix was created. Comparing to the original schedule, it had a savings of 202 days for this portion of the work. This interior work was not on the critical path, so it likely would not have a significant impact on the overall schedule but would present other schedule benefits. The cost estimates were calculated using RS Means data. Comparing the estimates, the SIPS matrix would have a labor cost savings of approximately $137,000. In addition, SIPS would lessen the congestion in the areas, make the work safer, and ease worker frustrations. It was recommended that SIPS be utilized for the residential unit work for Confluence.
Research: Target Value Design
Due to Confluence’s high number of add-ons and change orders, Target Value Design was used as a research topic. TVD is a practice that seeks to avoid the design-estimate rework cycle and to integrate cost and value as input into the design process. A survey was conducted to learn more about the industry’s knowledge of TVD as well as the benefits and negative outcomes of using it on a project. The results show that TVD is likely to increase overall team collaboration and commitment, but it will not necessarily decrease the actual cost. Considering that this project team is new to working together, it was not recommended to utilize Target Value Design for the Confluence project. However, if the same project team was able to implement more lean principles in the future, TVD could be considered for a succeeding project.